Phase In/Out in Inventory Management
Overview
In inventory management, the phase in/out process refers to
the transition of a new part from initial setup to becoming readily available
for stock orders. Understanding the phase in/out status of inventory parts is
crucial for maintaining efficient inventory levels and ensuring that only
actively used parts are stocked.
You can set the initial parameters by going into the parts
setup window under groups tab, in there you will find the Phase In/Out tab.
Phase In Status
- When
a new part is added to the inventory system, it enters a phase in status,
indicating that it is newly introduced and has limited historical data.
- During
the phase in status, the system monitors the part's usage patterns,
including average demand per month and total bin trips per month, to
evaluate its activity level. ("bin trips per month" refers to
the frequency with which a particular inventory item is being moved in and
out of storage bins within a given time period. This metric helps assess
the activity level or demand for the item and may influence its transition
from a new status to a current status within the inventory management
system).
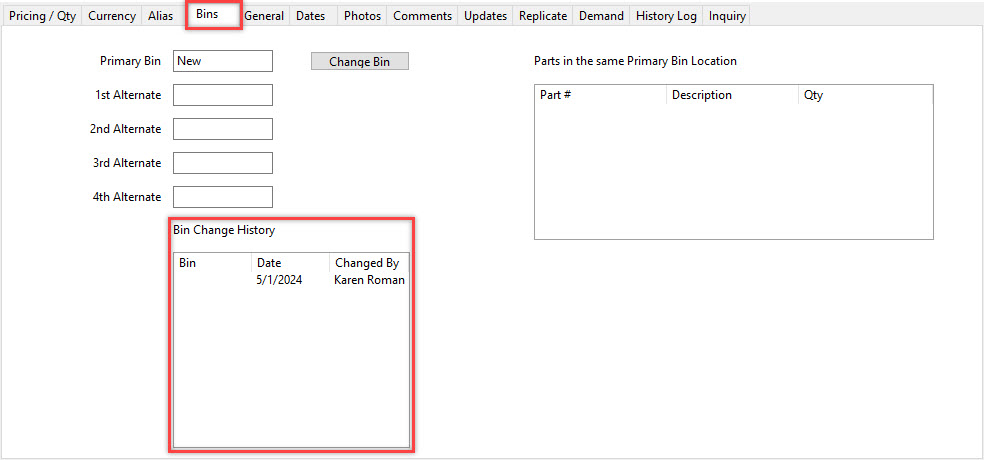
Transition to Current Status
- For a
part to transition from phase in to current status, it typically needs to
demonstrate sufficient activity, such as a minimum number of movements or
sales within a specified time frame.
- The
specific criteria for transitioning to current status may vary depending
on the organization's inventory management policies and practices.
Current Status
- Parts
in current status are considered actively used and are available for
automatic stock orders.
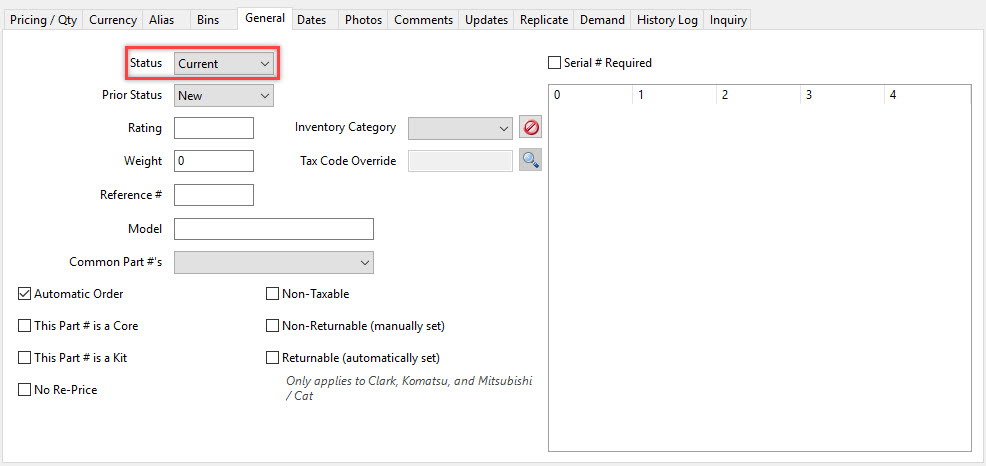
- Managers
rely on parts in current status for regular stock replenishment to meet
demand and maintain optimal inventory levels.
Monitoring Status
- Inventory
managers can monitor the status of parts by accessing the general tab in
the inventory system, where they can view the current status as well as
any prior status changes.
- It's
essential to regularly review and update the status of inventory parts to
ensure accurate stock management and prevent unnecessary ordering of
inactive or low-demand parts.
Auto Stock Feature
- The
auto stock feature automates the process of generating stock orders for
parts in current status to maintain adequate inventory levels.
- Parts
must be in current status for the auto stock feature to function
correctly, ensuring that only actively used parts are included in stock
orders.
Conclusion
Understanding the phase in/out process is essential for
effective inventory management, allowing organizations to maintain optimal
inventory levels, minimize stockouts, and improve overall operational
efficiency. By monitoring and managing the status of inventory parts,
businesses can ensure that resources are allocated efficiently, and inventory
costs are optimized.
Related Articles
Physical Inventory
Before starting the Physical Inventory Count process in Softbase, you will first want to run a report to capture the inventory counts and values. To do that in Softbase, on the Reports tab, run the following Report: Parts Inventory Valuation ...
Re-price Functionality in Inventory Management
Overview In inventory management systems, the "Re-price" functionality allows users to update the cost and list prices of parts based on the information provided in OEM price lists from vendors. It streamlines the process of adjusting prices in ...
Serialized parts inventory
When selling a serialized part, you will first need to create the part number that will be serialized in the parts setup. One the general tab, ensure you flag this part as serialized. Then, as you receive in each serialized part number will need to ...
Parts Inventory Reconciliation (not using WIP)
To reconcile inventory, there are a few variables that need to be considered when looking at your physical valuation when comparing it to the GL account balance. First, the costing method being used to value inventory will be either replacement cost ...
We would like to switch to using the FIFO method to value our inventory.
If you are currently using the replacement cost method and would like to update your system to use the FIFO method, you will want to take the following steps in Softbase: First, you will want to switch the warehouses to reflect the FIFO costs. This ...